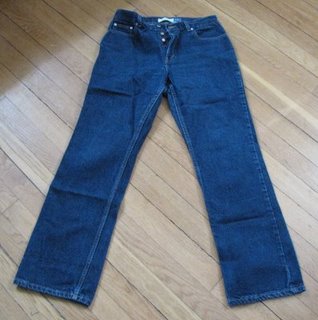
These jeans are pretty great, with the exception, of course, that they are about 2 sizes too small. On the plus side though, they are in great condition, they have the right length inseam for me, they have a button fly (which I love), and they are boot cut, so I won't have to add any additional width at the bottom to account for tapered jeans. They're also FREE, having been in my attic since I got pregnant with my 6 year old.
Incidentally, if you're not a denim hoarder like me, you can also do this with any pair of old jeans from the thrift store. In this economy, who wouldn't love to be able to walk into a store, pick up pretty much any pair of second-hand jeans in the store and know they could make them work?
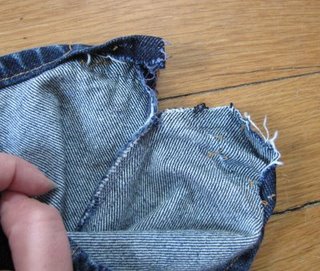
The first thing to do is to rip out the outseams with a seam ripper. I do this exactly the way your sewing instructor told you NOT to rip out seams. I put the seam ripper between the two sides of denim and cut the threads. Since the jeans have been sewn together with a chain stitch, you should be able to get enough play to just pull and rip without ripping a hole in the denim....and heck, it's quicker.
Cut all of the stitching on both sides from the beginning of the waistband to the hem. At the hem, tear out the stitches a few inches to either side of the seam and unroll the hem around the outseam.
Once your seams are ripped out, remove the stitches and left over thread pieces. Do NOT press the jeans after doing this. At the waistband, cut the waistband straight up from the seam.
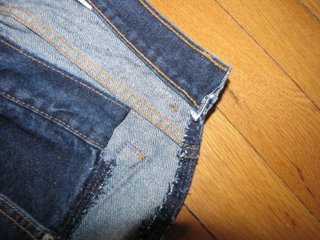
At this point, measure the outseam of the pants INCLUDING the extra fabric from the unrolled hem, but NOT including the waistband. This will be measurement A.
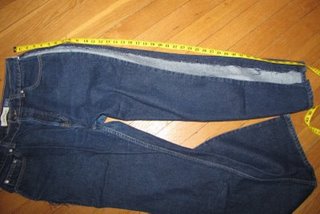
Additionally, measure the width of the waistband.
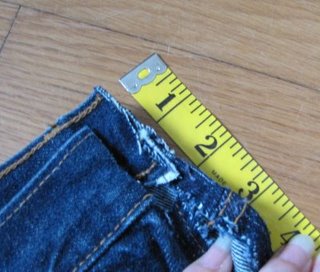
Then, try on the pants. Yes, post rip. Now you can get them on. The way I like to do this is by running a belt through the belt loops and tightening it so it hits at my waist.
Straighten out the jeans so the seams are in the right place and measure how much space there is between the outseams. Measure in a few different places along your hips, thighs, and waist, and be sure to measure on both sides. One measurement will be the largest. Use that one to give you an idea of how wide your side panels will have to be, as you can see in my picture here.
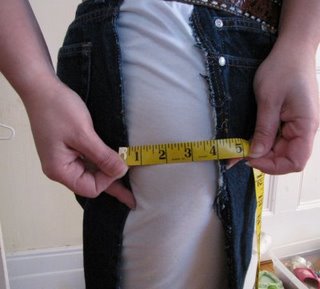
I need about 4" at the lower hip. For the panel I need to make, I will add 1" for seams and an additional 1" for comfort, for a total of 6" of width. This will be measurement B.
Note: this is a good time, if you want to, to add any appliques, embroideries, or other embellishments to your jeans. Now, you know how large the side panels of your pants will need to be. (A long, by B wide). The easiest way to do this is to cut a single piece of fabric to that measurement. I, however, tend to prefer to make a patchwork panel for the sides of my jeans, so that is what I will be showing.
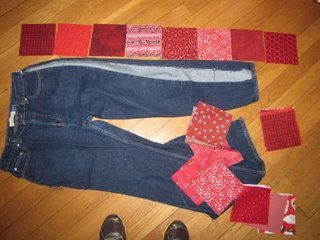
I start off by laying out the patches for my pants to get a good idea of how they will look. I then sew the patches together. Since the patches are cotton, and cotton is lighter weight than denim, I like to also add a lining piece of fabric for the inside of the jeans. This adds weight and also increases the durability of the panels.
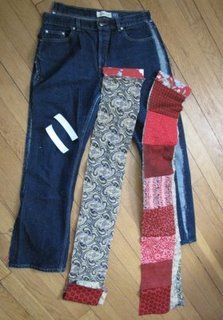
For the waistband, I take a piece of fabric the width of the panels and twice the length of the waistband plus 1" for seams. I fold the fabric lengthwise and place the raw edges lined up with the top of the panel going into the side of the pants. If you are using a lining piece, line this piece up also, matching the wrong side of the lining to the wrong side of the panel with the waistband piece on the outside, sandwiching the panel piece.
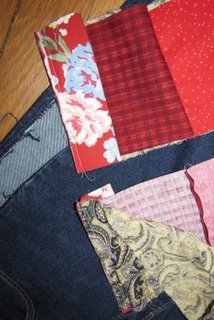
Additionally, I like to have a small piece of heavy duty elastic to add to the inside of the waistband. This helps pull in the waist from the comfort inches I added into the pants earlier.
I cut a piece of elastic 1" smaller than the actual measurement I needed from the pants when I measured them (for me this is 3"). If you prefer not to have elastic in your waistband, make the waistband the actual width you needed added to your jeans plus 1" for seams, and taper out from the waistband measurement along the sides of the panels until you get to the full width of the panels at approximately 3-4" below the waist. I prefer the elastic because it allows for "fat days" and slight weight fluctuations.
Line up the elastic with the center of the waistband, pin right sides together, and sew your side panel onto your jeans. The easiest way to do this is to have the jeans on top going through the sewing machine, and sewing right along the old seam line. The jeans should still have a slight fold where the old seam was. Just slowly follow along in this. No worries about the different coloration from the dyeing of the denim showing,and the jeans will automatically press to the side after stitching so they lie flat.
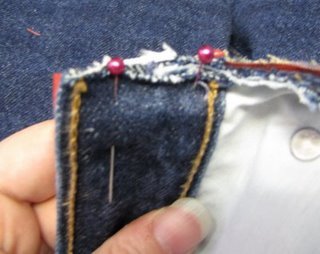
You will need to be careful when sewing around the rivet. Just go slowly and make sure you don't try to actually sew it. It should be off to the side, but in some jeans it is close.
Once you reach the hem, you may have some fabric left--cut that off straight across. Then sew on the other side of the panel, again with the jeans on top. Stop right before you hit the waistband on the way up, pull the elastic through the casing, and sew everything together. It should look like this when you are done:
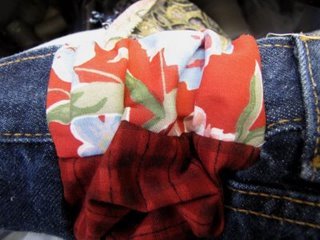
Repeat with the other side.
Once the side panels are all sewn in, I like to finish the seams. This will keep them from unraveling. I have a serger so I just serge the edges of the seams, just as they were before I ripped out the side seams of the jeans. If you don't have a serger, you can zig-zag along the raw edge, or you can use an over cast stitch if your machine has one.
For the hem, re-roll the jeans back to how they were originally rolled. The panel will start to roll for you. Just follow that roll all the way across, top stitch following the old hem seam, and you are done.
To troubleshoot length: If your jeans are NOT the correct inseam length, there are a few ways to work through this. If the pants are too short, measure how much additional length you need. you can either cut off the hem, and sew a length of fabric onto the bottom for this extra length as an easy fix, or you can use this more complicated method: After opening the outseam, but before measuring for the needed length of the panel, cut the measurement of the additional length you need above the hem plus one inch off the hem off the jeans. For example, if you need 3 extra inches, cut your jeans off 4" above the factory hem.
With the jeans open, sew a strip of fabric that is the extra length you need plus 1" for seams onto the bottom. Then sew on the hem of the jeans. Finish the jeans as above.
Try on your new jeans and give yourself a pat on the back.
One other trouble shooting tip: If your jeans are tapered at the ankle, you can counter that by tapering the bottom of your side panel so the bottom of your jeans is nice and straight...and along those same lines, if you like flares, just flare the panel as much as you want. Above all, feel free to experiment!
Another great thing about these jeans: If you get tired of the way they look, or if you lose or gain weight so they no longer fit again, you can just rip out the panels and start all over again! Good luck and Enjoy your new wardrobe!